www.sick.com
1800 334 802
sales@sick.com.au
Custom Solutions for Quality Control Systems in Primary Food and Beverage Packaging
click the images to find out more
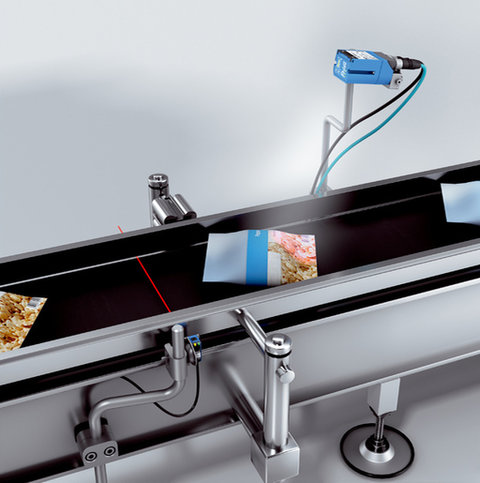
Check of codes on packaging
The use-by and expiration dates must be printed on packaged foods. Missing or illegible printouts result in defective or recalled products. Missing or incorrect information also presents health risks for consumers. The variable data and codes on the packaging must be systematically checked for quality and accuracy. The Inspector 2D vision sensor is the intelligent solution for this application. It compares and verifies codes or cleartext. Predefined tools simplify the application and inspection.
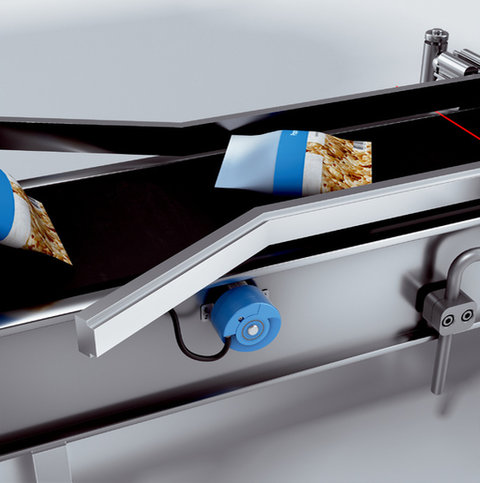
Determination of the speed of a belt
The conveyor belt speed needs to be determined for accurate control of the transport distance between packages. This is necessary in a variety of machines. Potato chips are fed into the machine from above. The packing film is removed from a roll, shaped, and sealed. A conveyor belt then transports the packaged product to the following process step. The transport speed determines the distance between the packages and, therefore, the process clock. A DFS60 incremental encoder, which is fitted directly to one of the conveyor belt shafts, records the speed of the belt in order to control the distance between products. The encoder is available with the TTL and HTL interfaces and as a programmable variant.
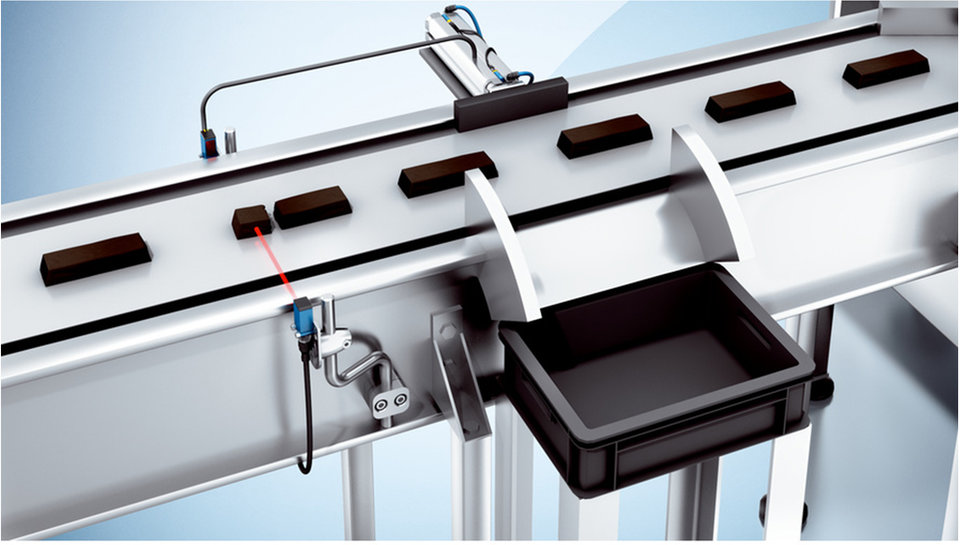
Integrated object and gap measurement when feeding products
When feeding products into horizontal forming, filling or sealing machines, it is necessary to check that the object being transported is of the correct size, and located in the correct position on the conveying equipment. When using the W4S-3 smart sensor and the integrated “Object and Gap Monitor” smart task, objects and gaps are identified directly within the sensor. Should any deviations in the expected values arise, the smart sensor sends appropriate signals to the controller. Thanks to the integrated signal delay and signal buffering functions, it is also possible for the sensor to directly control an actuator and thereby efficiently and autonomously remove faulty products.
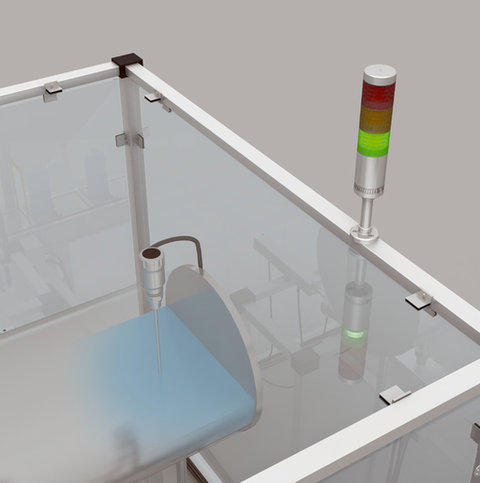
Level measurement in the machine tank of bottling machines
The level measurement in buffer tanks is a key application in bottling machines. The correct level must be measured in order to ensure the liquid supply to the bottling systems. The LFP Inox level sensor reliably distinguishes between liquid media and foaming. Using FDA-compliant materials, EHEDG-certified design, and CIP and SIP resistance, the LFP Inox is suitable for applications with stringent hygiene requirements.
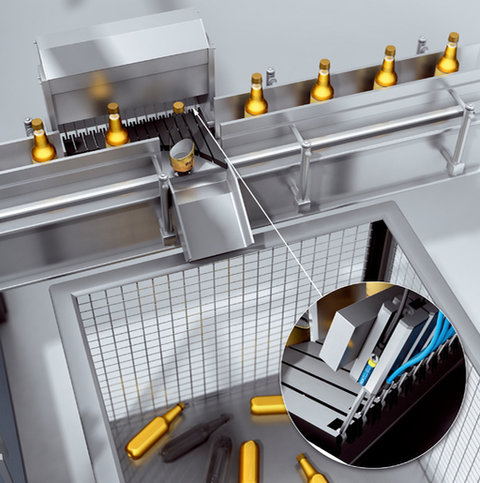
Removal of faulty products
Products identified during the bottling or labeling process as faulty must be reliably removed before they reach the packing stage. MZT7 sensors for T-slots are used on the pneumatic cylinders. The small magnetic cylinder sensors monitor the end positions of the cylinder so they can indicate the correct ejection movement.
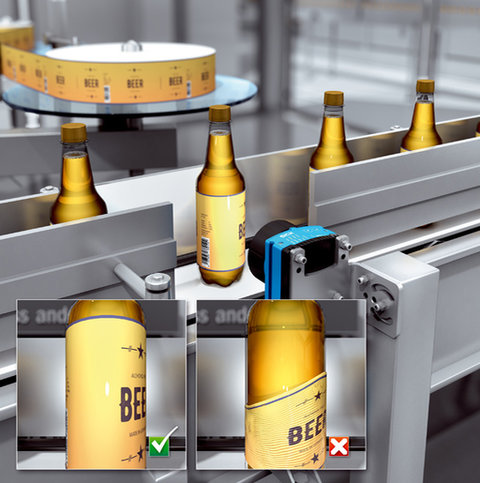
Check of the applied label
The label provides customers with information about the product and acts as an advertising platform too. Therefore, the programmable InspectorP632 Flex 2D vision checks for presence, position, and contents, e.g., product codes and symbols. The integrated web server provides a perfect overview of the functionality and inspection results via Ethernet.
Step up your game with SICK "3D Belt Pick"
SICK AppSpace eco-system provides intelligent software tools and algorithms that make developing SensorApps a breeze.
The use-by and expiration dates must be printed on packaged foods. Missing or illegible printouts result in defective or recalled products. Missing or incorrect information also presents health risks for consumers. The variable data and codes on the packaging must be systematically checked for quality and accuracy. The Inspector 2D vision sensor is the intelligent solution for this application. It compares and verifies codes or cleartext. Predefined tools simplify the application and inspection.
The conveyor belt speed needs to be determined for accurate control of the transport distance between packages. This is necessary in a variety of machines. Potato chips are fed into the machine from above. The packing film is removed from a roll, shaped, and sealed. A conveyor belt then transports the packaged product to the following process step. The transport speed determines the distance between the packages and, therefore, the process clock. A DFS60 incremental encoder, which is fitted directly to one of the conveyor belt shafts, records the speed of the belt in order to control the distance between products. The encoder is available with the TTL and HTL interfaces and as a programmable variant.
When feeding products into horizontal forming, filling or sealing machines, it is necessary to check that the object being transported is of the correct size, and located in the correct position on the conveying equipment. When using the W4S-3 smart sensor and the integrated “Object and Gap Monitor” smart task, objects and gaps are identified directly within the sensor. Should any deviations in the expected values arise, the smart sensor sends appropriate signals to the controller. Thanks to the integrated signal delay and signal buffering functions, it is also possible for the sensor to directly control an actuator and thereby efficiently and autonomously remove faulty products.
The level measurement in buffer tanks is a key application in bottling machines. The correct level must be measured in order to ensure the liquid supply to the bottling systems. The LFP Inox level sensor reliably distinguishes between liquid media and foaming. Using FDA-compliant materials, EHEDG-certified design, and CIP and SIP resistance, the LFP Inox is suitable for applications with stringent hygiene requirements.
Products identified during the bottling or labeling process as faulty must be reliably removed before they reach the packing stage. MZT7 sensors for T-slots are used on the pneumatic cylinders. The small magnetic cylinder sensors monitor the end positions of the cylinder so they can indicate the correct ejection movement.
The label provides customers with information about the product and acts as an advertising platform too. Therefore, the programmable InspectorP632 Flex 2D vision checks for presence, position, and contents, e.g., product codes and symbols. The integrated web server provides a perfect overview of the functionality and inspection results via Ethernet.