The technology involved in product inspection has become increasingly sophisticated. Vision inspection and x-ray detection have been added to the more traditional metal detection and checkweighing options. But for the busy production manager, intent upon delivering quality product on time while protecting the bottom line, many of the technological advancements in product inspection can seem rather remote from the challenges they are facing daily.
This is something that Mettler-Toledo has been keen to address by understanding the key production drivers, and addressing these with our latest x-ray inspection systems.
Addressing customer diversity
Enthusiasm for the latest technological developments can be variable: and it has sometimes been the case that the aspirations of the equipment manufacturer have failed to align with those of the customer. Put simply, it doesn’t matter how many bells and whistles you can offer, if none of them resonate with the realities of the production line.
It can be difficult for equipment manufacturers to determine what the customer wants, because their needs are so diverse. For example, the customer could be a global food brand that produces 150 different products in a year. This equates to 150 changeovers that could limit production capacity. In this production environment, the emphasis is likely to be on ease and swiftness of changeovers. This is but one example, so we've looked at some key production drivers that are common to most production environments, whatever the size of operation.
Key drivers
Uptime
For food manufacturers, the consequences of an outage can be severe: resulting in significant loss of product, not just production time. For example, bread dough may not bake properly if the proving process is interrupted, and frozen beef burgers may thaw on a stationery conveyor while an emergency repair is made further down the line.
Quality
Contributing factors to delivering quality include conformance with any legislative and brand requirements, the ability to produce the same product consistently time after time and the requirement to avoid physical contamination. Failure in any one of these aspects could result in a product recall, which not only represents lost revenue, but also lost reputation.
Cost
Capital cost is only one factor that affects the decision to purchase product inspection equipment. Increasingly, customers are looking at other means of assessing the return on investment. These include operational requirements like energy consumption and maintenance frequency. There is also the issue of staff training. With complex machinery, it can be the case that a few employees understand all the technical intricacies of a piece of equipment. If they leave the business, that knowledge goes with them. As production inspection technology evolves, it is more important than ever that it is easy to use and does not require specialist knowledge to operate.
Putting production first
Mettler-Toledo has put these key production drivers first in developing its latest range of x-ray inspection systems, with the aim of ensuring that any technological advances are both appropriate and affordable.
For example, the X34 is a single lane x-ray system designed for the inspection of a wide range of small and medium-sized packaged products. It provides a combination of technologies which enable producers to detect smaller contaminants reliably at high-throughputs, ensuring product safety and delivering brand protection.
The system comes with advanced software that enables automated product set-up, dramatically decreasing the chance of human error. New products only need to be passed once through the system for the power to be optimised and the intuitive software requires minimal passes to automatically set the contamination inspection tools. All the instructions are given via a touchscreen: there is no need for the operator or the purchaser to acquire any special programming skills. This makes for more efficient and profitable operations.
To reduce operating costs, the X34 is equipped with an ‘Optimum Power’ generator, which automatically maximises detection sensitivity, and a 0.4mm detector for the accurate detection of very small contaminants, whether metal, high density plastics, glass, and stone or calcified bone, all while saving on power. ContamPlus™ software further enhances detection capabilities, helping manufacturers to achieve a zero False Reject Rate (FRR). This is a crucial means of reducing product waste and ensuring product safety.
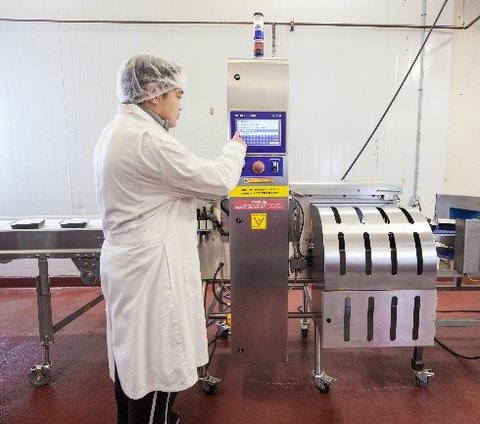
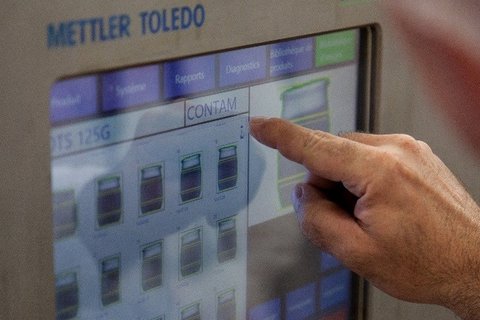
More than contamination detection
Product inspection equipment has much to offer busy production managers, beyond the basic requirements of contamination detection and compliance. Technological advances are being harnessed to address the key challenges of uptime, quality and cost using automation to eliminate human error, optimise performance and control energy consumption.
The optimized detection and automated set-up evident within Mettler-Toledo’s existing vertical x-ray range is a prime example. These systems are available as standard, ensuring that busy production managers have rapid access to the benefits that modern product inspection systems can bring.
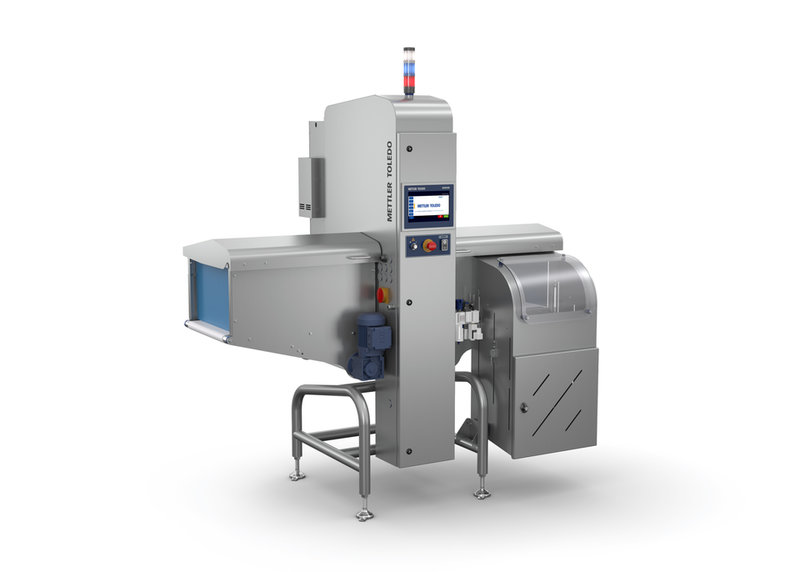