click on the bullets to read further
With flow simulation to an optimized design of the NEMO® progressing cavity pump
Scroll down to learn more ⤵
Cleanability within closed process plants and equipment with pumps is critical and crucial not only in the food industry. Positive displacement pumps are often – due to their construction – challenging to clean in the process, (CIP). Following a standardized cleaning test NETZSCH started its analysis of the NEMO® progressing cavity pump. These kind of pumps are often used for higher viscous media, which make a quick cleaning process challenging. The task for many users is to reduce production downtime and increase the ease and speed of interrupting processes such as cleaning.
NETZSCH Pumps & Systems, as leading manufacturer of positive displacement pumps and as partner of its customers considers science based procedures and methods such as real tests and computational fluid dynamics (CFD) to improve the fulfillment of these requirements. CFD has been proven as a tool which can be used by manufacturers to facilitate their equipment design for high hygienic standards even before constructing any prototypes or optimize an existing design. The study of hydrodynamic cleanability of closed processing equipment was used based on modelling the flow in a NEMO® progressing cavity pump. Results show that cleaning can be very efficient in complex geometries.
The degree of turbulences and type of flow pattern can be determined with CFD and tested with real pumps in the NETZSCH in-house test laboratory. Even though easy and reliably cleanable positive displacement pumps are on the market for many decades, there is still quite a large room for improvements and optimization. Beside the aim to construct the best cleanable pump with these proven methods NETZSCH also optimized the pump geometries towards gentle handling of the media by further improving the flow through the pump housing. Sustainable, safe production with less downtime and high quality results on pumping operation can be ensured.
With flow simulation to an optimized design of the NEMO® progressing cavity pump
Scroll down to learn more ⤵
Scroll down to learn more ⤵
Cleanability within closed process plants and equipment with pumps is critical and crucial not only in the food industry. Positive displacement pumps are often – due to their construction – challenging to clean in the process, (CIP). Following a standardized cleaning test NETZSCH started its analysis of the NEMO® progressing cavity pump. These kind of pumps are often used for higher viscous media, which make a quick cleaning process challenging. The task for many users is to reduce production downtime and increase the ease and speed of interrupting processes such as cleaning.
NETZSCH Pumps & Systems, as leading manufacturer of positive displacement pumps and as partner of its customers considers science based procedures and methods such as real tests and computational fluid dynamics (CFD) to improve the fulfillment of these requirements. CFD has been proven as a tool which can be used by manufacturers to facilitate their equipment design for high hygienic standards even before constructing any prototypes or optimize an existing design. The study of hydrodynamic cleanability of closed processing equipment was used based on modelling the flow in a NEMO® progressing cavity pump. Results show that cleaning can be very efficient in complex geometries.
The degree of turbulences and type of flow pattern can be determined with CFD and tested with real pumps in the NETZSCH in-house test laboratory. Even though easy and reliably cleanable positive displacement pumps are on the market for many decades, there is still quite a large room for improvements and optimization. Beside the aim to construct the best cleanable pump with these proven methods NETZSCH also optimized the pump geometries towards gentle handling of the media by further improving the flow through the pump housing. Sustainable, safe production with less downtime and high quality results on pumping operation can be ensured.
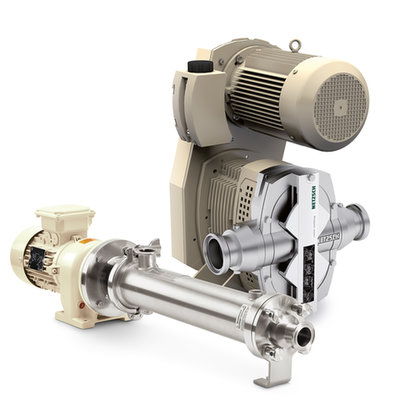
The major differences to industrial pumps are covering the choice of the food-grade materials for all product-wetted parts as well as the finish of the surfaces, no dead areas in the pump housing and no crevices as open joints are permanently flushed or alternatively used flexible rods are shrunk to the rotor avoiding any wear.
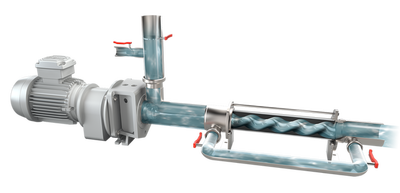
To achieve the necessary velocity of flow for the cleaning fluid of at least 1.5 m/s in the entire system in accordance with CIP and SIP procedures Hygienic and Aseptic Pumps are equipped with additional flushing ports in tangential configuration and a bypass line. Complete emptying of the pump is guaranteed. All pump materials are suitable for CIP and SIP processes
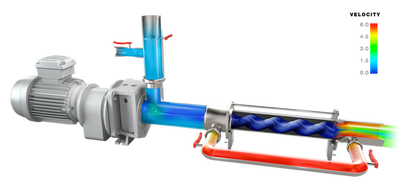
The required 1,5 m/s is even reached in the large pump housing part. The velocity in the other parts, such as by-pass and discharge flange is even far higher.
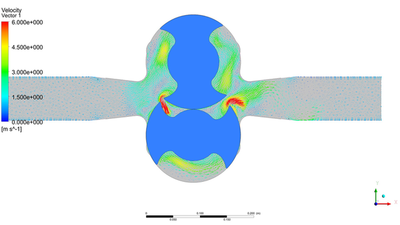
“The devil is in the detail or “it´s the little things that cause big problems”. These so called little things are the challenges to overcome: with regards to gentle product handling and even more with regards to cleaning. The small and tiny dead ends and corners in a pump are demanding optimization or elimination. But these challenges could be solved by NETZSCH with CFD simulations and the results lead to huge advantages and most important safe and healthy operation of pumps in food and pharma applications.
Back to top ⤴
Back to top ⤴